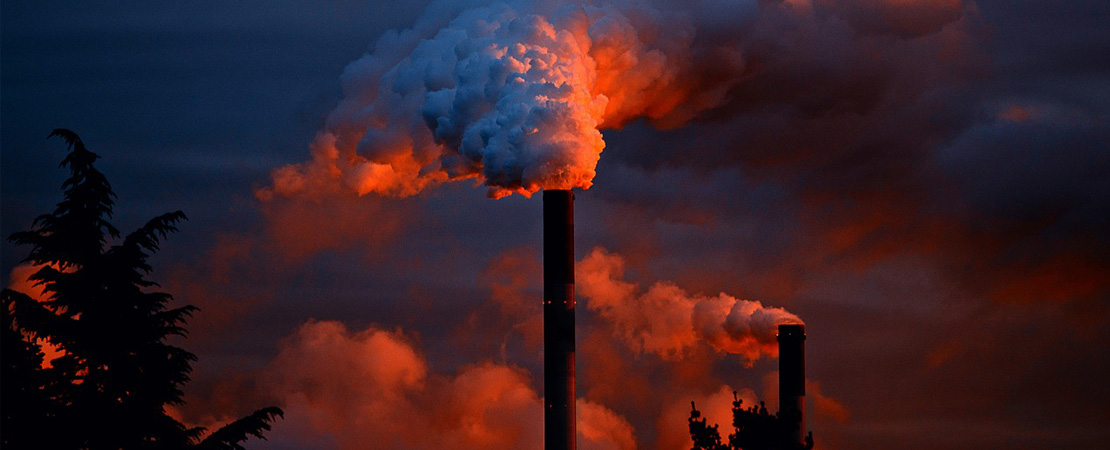
工場やビル、ビル管理などの設備は、いつ故障するかわかりません。
もし大切な機械が突然止まってしまったら、生産ラインが止まって大きな損失につながることもあります。
そこで注目されるのが「予知保全」です。
予知保全は、故障が起きる前に異常を見つけてメンテナンスを行う方法で、IoTと組み合わせることでより効果を高められます。
この記事では、IoTを活用した予知保全の具体的なステップを解説します。
- 目次
-
- 1.予知保全とは何?
- 2.センサー選定と設置ポイント
- 1.振動センサー
- 2.温度センサー
- 3.電流センサー
- 4.音センサー
- 3.データ収集から異常検知までのワークフロー
- 1.データ収集
- 2.データ蓄積(ストレージ)
- 3.前処理と特徴抽出
- 4.異常検知モデルの適用
- 5.レポートと可視化(ダッシュボード)
- 6.メンテナンス実施
- 4.導入時の注意点・効果
- 1.センサーの品質と配置
- 2.ネットワーク環境
- 3.モデルのチューニング
- 4.人とシステムの連携
- 5.期待できる効果
- 1.ダウンタイムの短縮
- 2.メンテナンスコストの削減
- 3.エネルギー効率の向上
- 4.安全性の向上
- 6.まとめ
予知保全とは何?
「予知保全」とは、機械や設備の故障をあらかじめ予測し、まだ壊れる前に部品の交換や調整を行うしくみです。
これまでの「故障してから修理する」や「定期的に交換する」といった方法に対し、予知保全は「いつ交換すればいいか」をデータに基づいて判断します。そのため、余計な部品交換を減らしてコストを削減できるだけでなく、予期せぬダウンタイム(停止時間)を防ぐこともできます。
IoTを使うと、センサーで機械の状態をリアルタイムに監視し、異常のサインをすぐにキャッチできるようになります。振動や温度、電流などのデータをクラウドに集めて解析し、異常検知や寿命予測を自動化できるのが大きなメリットです。
センサー選定と設置ポイント
予知保全に必要なのは、まず「なにを測るか」を決めることです。
振動センサー
モーターやベアリングの回転状態をとらえます。不自然な振動は部品のすり減りや歪みのサインです。
温度センサー
軸受け(ベアリング)やコイル、配管の温度を監視します。いつもより温度が上がっていると、摩擦や電気トラブルの予兆かもしれません。
電流センサー
モーターやポンプの消費電流を測ります。負荷が増えると電流が上がるので、詰まりや軸の異常を検知できます。
音センサー
高性能なマイクで異音をとらえます。金属同士がこすれる音やベアリングの異音は、故障の前触れです。
これらのセンサーは、異常を発見しやすい「ボトルネック」や「高負荷部位」に設置します。具体的には、モーターの本体近くや軸受けの外側、パイプの曲がり角などです。また、熱を持ちやすく人が触れない場所にはリモート温度計や赤外線センサーを使うと便利です。
データ収集から異常検知までのワークフロー
IoT×予知保全では、センサーで集めたデータをステップごとに処理します。
主な流れは、
①データ収集
②データ蓄積
③前処理と特徴抽出
④異常検知モデルの適用
⑤レポートと可視化
⑥メンテナンス実施
です。
1つずつ何をするか見ていきましょう。
データ収集
センサーが振動や温度、電流、音などのデータを1秒ごと、あるいは数秒ごとに取得し、ゲートウェイと呼ばれる装置を通じてクラウドへ送ります。
データ蓄積(ストレージ)
送られてきたデータは、クラウド上のデータベースに日付や時刻とともに記録されます。大量のデータを長期間保存し、あとで見返せるようにします。
前処理と特徴抽出
生データにはノイズ(余計な振動や雑音)がふくまれます。これをフィルターで取り除き、振動なら周波数スペクトル、温度なら平均値・最大値など、分析しやすい特徴量に変換します。
異常検知モデルの適用
過去の正常データと異常データをもとに作った機械学習モデルを使い、リアルタイムのデータを評価します。規定のしきい値(しきい値)を超えるとアラートが上がり、担当者に通知されます。
レポートと可視化(ダッシュボード)
データをグラフや表で見やすくまとめ、異常発生のタイミングや傾向を一目でわかるダッシュボードをつくります。複数の現場があれば、一つの画面でまとめて監視できます。
メンテナンス実施
アラートを受けたら、予定外の停止を避けるためにすぐメンテナンスを計画・実施します。部品交換や注油、調整作業を行い、正常状態に戻します。
導入時の注意点・効果
IoT×予知保全の導入で注意すべきポイントは以下のとおりです。
センサーの品質と配置
安価なセンサーでは誤検知やデータ欠損が起こりやすいので、信頼性の高いものを選びます。また、適切な場所に設置しないと、正しい異常サインをとらえられません。
ネットワーク環境
工場やビルの構造によっては、Wi Fiがとどきにくい場所があります。有線LANやセルラー回線、メッシュネットワークなど、現場に合わせた通信方式を選びましょう。
モデルのチューニング
異常検知モデルは、現場の環境や機器ごとに調整が必要です。初期設定だけでなく、運用しながらしきい値や学習データを見直すことが成功の鍵です。
人とシステムの連携
IoTはあくまで道具です。最終的に判断し、対応するのは人です。アラートと現場作業がスムーズに連携できる仕組みづくりが重要です。
期待できる効果
ダウンタイムの短縮
故障前に対応することで、生産停止やサービス停止の時間を大幅に減らせます。
メンテナンスコストの削減
必要なときだけ部品交換や調整を行えるため、余計な部品をストックせずにすみます。
エネルギー効率の向上
異常やムリな動きを早期に発見し、最適な運転をつづけることで、電気代の節約につながります。
安全性の向上
大きな故障の前兆をつかむことで、事故やケガのリスクをへらせます。
まとめ
IoTでの予知保全は、最初から完璧を目指す必要はありません。
たとえば温度センサー1台を導入し、2週間データを観察するだけでも大丈夫です。ぜひ、まずは手軽なセンサーから始めて、「次はどこを狙うか」を見極めてみてください。
IoTによる予知保全が、あなたの現場をもっと安心・効率的に変えてくれるはずです。
弊社では、IoT機器を販売・開発しております。ご相談やご質問をお待ちしております。お気軽にお問い合わせください。